Enzymes – an eco-friendly alternative for the textile industry?
With the increasingly important requirement for textile manufacturers to reduce pollution in textile production, the use of enzymes in the chemical processing of fibers and textiles is rapidly gaining wider recognition. Enzymes are non-toxic and eco-friendly. They can be safely used in a wide selection of textile processes such as de-sizing, scouring, bleaching, dyeing and finishing, where the traditional alternatives are very harsh chemicals whose disposal into the environment causes many problems.
The use of enzymes is not a new development. Enzymes play a diversified role in many aspects of everyday life. Enzymes are nature’s catalysts. Humankind has used them for thousands of years to carry out important chemical reactions for making products such as cheese, beer, and wine. Bread and yogurt also owe their flavor and texture to a range of enzyme producing organisms that were domesticated many years ago.
What are enzymes and do they do?
Enzymes are proteins with highly specialized catalytic functions, produced by all living organisms. Enzymes are responsible for many essential biochemical reactions in microorganisms, plants, animals, and human beings. Enzymes are essential for all metabolic processes, but are not alive. Although like all other proteins, enzymes are macromolecules composed of amino acids which have different functions. Enzymes have the unique ability to facilitate biochemical reactions, acting as catalysts without undergoing changes themselves. This catalytic capability is what makes enzymes unique. Enzymes are natural protein molecules that act as highly efficient and very selective catalysts in biochemical reactions. They help a chemical reaction to take place quickly and efficiently. Enzymes not only work efficiently and rapidly, they are also biodegradable. Enzymes are highly efficient in increasing the reaction rate of biochemical processes that otherwise proceed very slowly, or in some cases, not proceed at all. [1]
What Types of enzymes are there?
Enzymes are categorized according to the compounds they act upon. Some of the most common ones include:
- Proteases, which break down proteins
- Amylases, which break down starch into simple sugar molecules
- Cellulases, which break down cellulose
- Lipases, which split fats (lipids) into glycerol and fatty acids
Thermodynamics
Like all biocatalysts, enzymes speed up biochemical reactions by lowering the activation energy, which must be overcome to complete a chemical reaction. As a result, products are formed faster at milder conditions (lower temperatures), and chemical reactions reach their equilibrium state more rapidly. Most enzyme reaction rates are millions of times faster than those of comparable un-catalyzed reactions. As with all catalysts, enzymes are not consumed by the reactions they catalyze, nor do they alter the equilibrium of these reactions. However, enzymes do differ from most other catalysts in that they are highly specific for their substrates. [2]
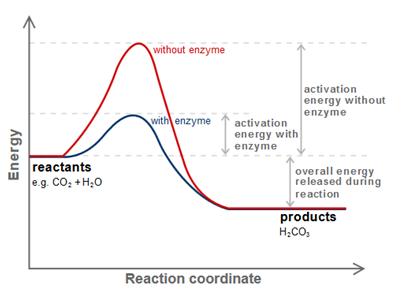
In chemistry, the activation energy is a term introduced in 1889 by the Swedish scientist Svante Arrhenius. It is defined as the minimum energy that must be input to a chemical system, containing potential reactants, in order for a chemical reaction to occur. Activation energy may also be defined as the minimum energy required starting a chemical reaction. The activation energy of a reaction is usually given in units of kJ/mole (kilojoules per mole).[3]
Enzymes do not alter the position of the chemical equilibrium of the reaction. Usually, in the presence of an enzyme, the reaction runs in the same direction as it would without the enzyme, just more quickly. The catalytic activity of an enzyme is based only on the ability to reduce in a chemical reaction the activation energy. This is the energy content, which must be invested to start up a reaction.
The enzyme stabilized the reaction by non-covalent interactions in the state of transition, so that less energy is necessary to bring the substances in the transition state. The substance can metabolize much quicker to the reaction product, because the way is quasi flattened.[4]
However, in the absence of the enzyme, other possible un-catalyzed, “spontaneous” reactions might lead to different products, because in those conditions this different product is formed faster.
Enzymes equally catalyze the forward and backward reactions. They do not alter the equilibrium itself, but only the speed at which it is reached. For example, carbonic anhydrase catalyzes its reaction in either direction depending on the concentration of its reactants.
High concentration of CO2:
Low concentration of CO2:
Nevertheless, if the equilibrium is greatly shifted to one direction, in a very exergonic reaction, the reaction is in effect irreversible. Under these conditions, the enzyme will, in fact, catalyze the reaction only in the thermodynamically allowed direction.4
The active centre – structural background for catalysis and specificity
The basic mechanism by which enzymes catalyze chemical reactions begins with the binding of the substrate (or substances) to the active centre (site) on the enzyme. This active site is the specific region of the enzyme which combines with the substrate (enzyme-substrate-complex). The binding of the substrate to the enzyme causes changes in the distribution of electrons in the chemical bonds of the substrate and ultimately causes the reactions that lead to the formation of products. The products are released from the enzyme surface to regenerate the enzyme for another reaction cycle. The active site has a unique geometric shape that is complementary to the geometric shape of a substrate molecule, similar to the fit of puzzle pieces. This means that enzymes specifically react with only one (or a very few similar structurally related compounds).[5] Illustrative fits only one specific substrate to the corresponding enzyme like a key to a lock (Lock and key model). That is the reason for the high substrate specificity of enzymes.
key-lock mechanism of enzyme catalysis
Also, the active site continues to change until the substrate is completely bound, at which point the final shape and charge is determined.[7] Induced fit may enhance the fidelity of molecular recognition in the presence of competition and noise via the conformational proofreading mechanism.[8]
Sometimes take two substances part to the reaction. The enzyme guarantees in these cases the right orientation of the reacting agent. This peculiarity of the enzymatic reaction is the basis of the conformational proofreading mechanism.
Catalytic Mechanisms
Enzymes can act in several ways, all of which lowers activation energy (ΔG‡):[9][10]
- Lowering the activation energy by creating an environment in which the transition state is stabilized
- Lowering the energy of the transition state, without distorting the substrate, by creating an environment with the opposite charge distribution as the transition state.
- Providing an alternative pathway. For example, temporarily reacting with the substrate to form an intermediate ES complex, which would be impossible in the absence of the enzyme
- Reducing the reaction entropy change (ΔS‡) by bringing substrates together in the correct orientation to react. Considering heat of reaction (ΔH‡) alone would overlook this effect.
- Increases in temperature speed up reactions. Thus, temperature increases help the enzyme function and develop the end product even faster. However, if heated too much, the enzyme’s shape deteriorates and the enzyme becomes denatured. Some enzymes like thermo labile enzymes work best at low temperatures.
- The function of a protein is dependent on its three-dimensional physical structure. So, if the structure is disrupted, the function is disrupted as well.
Enzyme kinetics
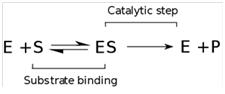
Enzyme kinetics is the investigation how enzymes bind substrates and convert them into products. The enzyme reaction works in two stages. In the first stage, the substrate binds reversibly to the enzyme, forming the enzyme-substrate complex. This is sometimes called the Michaelis complex. The enzyme then catalyzes the chemical step in the reaction and releases the product.[11] The reaction speed depends on the change of the substrate concentration over time, for the amount of substance or substrate, which transfers a certain reaction volume per time unit (unit: mole/(l*s)). Besides reaction conditions like temperature, salt concentration and pH value of the solution, the reaction rate depends on the enzyme concentration, the substrate, products and activators or inhibitors.
Conditions that denature the enzyme (protein) abolish its activity, such as high temperatures, extremes of pH or high salt concentrations, while raising substrate concentration [S] tends to increase the activity when [S] is low. To find the maximum speed of an enzymatic reaction, the substrate concentration is increased until a constant rate of product formation is seen.
Enzyme kinetics, according to Michaelis-Menten, relies on the law of mass action, which is derived from the assumptions of free diffusion and thermodynamically driven random collision. However, many biochemical or cellular processes deviate significantly from these conditions, because of macromolecular crowding, phase-separation of the enzyme/substrate/product, or one or two-dimensional molecular movement.[15]In these situations, fractal Michaelis-Menten kinetics may be applied.[16]
How are enzymes preparations made?
The first step in producing enzymes is to identify the optimal organism or host. The most common approach is to investigate plants and microorganisms found in nature, where enzymes may already be doing what is desired for an industrial application. There is a rich and broad variety of life on earth, particularly involving microorganisms. These naturally occurring enzymes are quite often not readily available in sufficient quantities for food applications or industrial use.
Newer approaches work with existing microorganisms and apply genetics engineering or molecular biology methods to incorporate new features into the protein structure so that new, desired enzyme properties can be obtained in the lab. Ultimately, industrial enzymes are produced by fermentation, similar to the production of beer or wine. The organisms are fermented using a suitable nutrient and controlled conditions to produce the enzymes, through either intracellular or extracellular expression. Once fermentation is completed, the microorganisms are destroyed; the enzymes are then separated through centrifugation or filtration and stabilized to maintain suitable shelf lives. Collectively, these approaches have created a large variety of enzymes available for industrial use – and the list grows longer every day.[17]
- Increased efficiency of enzyme production resulting in higher yields;
- Increased enzyme purity through reduction or elimination of side activities;
- Enhancing the function of specific enzyme proteins, e.g., by increasing the temperature range over which an enzyme is active.
The results are better products, produced more efficiently, often at lower cost and with less environmental impact.
It wasn’t until genetic engineering came up, that these biological methods became economically viable. Targeted genetic manipulation has not only enhanced the productivity of these methods, it also has resulted in the production of substances that were previously impossible. To date, up to 60% of all technical enzymes are produced with genetically modified organisms (GMO) – and this number is sure to increase given that GMO-based enzyme production requires 40-50% less energy and raw materials than traditional enzyme production.[19]
Advantages & disadvantages of enzymatic textile processing:
Textile manufacturing processes, due to the particular properties of enzymes, can be operated in a are much more environmentally friendly way. In summary, this implies:
- Enzyme- catalyzed reaction are faster than chemically-catalyzed reactions. While compared to the un-catalyzed reactions, enzymes typically enhance the reaction rates by 106-1013 times[20].
- Enzyme catalyzed reactions run under mild conditions, with respect to temperature (far below 100°C), pressure (atmospheric) and pH (around neutral pH value), because the enzymes reduce the activation energy significantly, resulting in lower energy costs.
- Shorter processes and less rinse bathes help to reduce water consumption
- Enzyme catalyzed reactions are easy to control. They do not attack the fiber structure with resulting loss of weight, resulting in better quality of the material
- Enzymes are bio-degradable (less or no impact on environment)
- Enzymes have far greater reaction specificity than chemically-catalyzed reactions and they rarely form by-products. The high substrate specificity of enzymes is due to the individual architecture of the active site where only certain molecules can stereo-fit in
- Saving in chemicals and energy has less or no impact on the environment (less B.O.D, C.O.D and TDS).
- Contribute to safer working conditions through elimination of chemical treatments during production processes
On the other hand, there are few disadvantages of enzymes application in textile processing. Some physical and chemical factors affect the stability of enzymes. Many of the disadvantages can be reduced with simple actions:
- The process continues until the enzyme is deactivated
- Enzyme processes can deactivated easily by increasing the pH value and/or the temperature
- Most of the enzymes are usually active over narrow range of pH and temperature, so need to maintain the temperature and pH.
- In modern machinery the steering of the temperature is no problem, especially at the lower temperature, which the enzymes need. A constant pH value can be achieved by a good buffering system. Most enzyme products include such a system in their formulation
- Once destroyed , they cannot be reactivated
- This is mostly a problem of the transportation and in some countries with high temperatures. In both cases the enzymes must be stored under 20 °C – ideally at 5 °C.
- Certain alkalis, antiseptics and acid liberating agents tend to inhibit the enzyme activity
- The inhabitation with alkalis and acid agents can solved by a good buffering system; antiseptics are normally not used in the textile wet processing
- Some enzymes (proteolytic) may cause irritation (skin and eyes), respiratory allergies
- All enzyme products must be handled with care. Most enzyme producers coat there enzymes to prevent dust problems during the processing stage.
- For the consumers there is no irritation, because on the finished product the (activated or deactivated) enzymes are washed off
- Certain enzymes require specific bivalent metallic ions (Ca2+, Mg2+, Fe2+, Mn2+) as activators to stabilize enzyme substrate complex or by sensitizing substrate to the attack of enzymes
- Most of the enzymes used in the wet processing (exception the activator for laccase) do not use metallic ions
Conclusion
Chemical oriented textile wet processing is a the pollution causing process in the textile mills contributing to the maximum of the total BOD, COD and TDS load in effluent. Textile manufacturers use a number of acutely toxic chemicals, including heavy metals, formaldehyde and aromatic solvents, many of which are classified as hazardous by the World Health Organization (WHO) and have been associated with cancer, birth defects and hormonal and reproductive effects in wildlife and humans.
Responding to increasing consumer concerns about health and environment, businesses are now seeking ways to make products in the most environmentally sensitive way. The use of enzymes in the textile industry is an example of industrial biotechnology, which allows the development of environmentally friendly technologies in processing and strategies to improve the final product quality. The consumption of energy and raw-materials, as well as increased awareness of environmental concerns related to the use and disposal of chemicals into landfills, water or release into the air during chemical processing of textiles are the principal reasons for the application of enzymes in textile processing. Enzymes gives the retailers of the ZDHC project a good opportunity to reduce the harmful chemicals out of there production chain. Parallel to the reduced problems with waste water they have a cost-saving effect by less water and energy consumption.
One example of a long term enzyme use is the application of amylases. They have been used for desizing since the middle of the last century. Before the discovery of amylase enzymes, the only alternative to remove the starch-based sizing was extended treatment with caustic soda at high temperature.
The chemical treatment was not totally effective in removing the starch (which leads to imperfections in dyeing) and also results in a degradation of the cotton fiber resulting in destruction of the natural, soft feel, or hand, of the cotton. The use of amylases to remove starch-based sizing agents has decreased the use of harsh chemicals in the textile industry, resulting in a lower discharge of waste chemicals to the environment, improved the safety of working conditions for textile workers and has raised the quality of the fabric.[21]
Outlook
This report shows an overview of the technical, physical and chemical advantages using enzymes. At present, the enzymes used most frequently are for cotton products (especially denim), but there are also enzymes used for the wet processing of other natural fibers (wool, silk) and synthetic fibers (polyester, polyamide). Currently researchers and developers seek to produce new enzymatic products and processes, which are more efficient and cost-saving. Moreover, they try to combine single steps to useful combinations, which should reduce the processing time, water and energy consumption more and more. This should allow a broad use of biotechnology method in the textile processing and hence for environmental products and processes with better functionality and quality.
[1] fibre2fashion.com: Enzymes in textile industry
[2] Bairoch A. (2000). “The ENZYME database in 2000” (PDF). Nucleic Acids Res 28 (1): 304–5. doi:10.1093/nar/28.1.304
[3] Dunning,D. in ehow.com: What Is Activation Energy?
[5] Elmhurst.edu: Mechanism of Enzyme Action
[7] Boyer, Rodney (2002) [2002]. “6”. Concepts in Biochemistry (2nd ed.). New York, Chichester, Weinheim, Brisbane, Singapore, Toronto.: John Wiley & Sons, Inc. pp. 137–8. ISBN 0-470-00379-0. OCLC 51720783
[8] Savir Y & Tlusty T (2007). “Conformational proofreading: the impact of conformational changes on the specificity of molecular recognition”. In Scalas, Enrico. PLoS ONE 2 (5): e468. doi:10.1371/journal.pone.0000468
[9] Fersht, Alan (1985). Enzyme structure and mechanism. San Francisco: W.H. Freeman. pp. 50–2. ISBN 0‑7167 1615-1
[10] Jencks, William P. (1987). Catalysis in chemistry and enzymology. Mineola, N.Y: Dover. ISBN 0-486-65460-5
[11] http://www.wiley.com/college/pratt/0471393878/student/animations/enzyme_kinetics/index.html
[13] Taylor, K.B., Enzyme kinetics and mechanisms
[15]Ellis RJ (2001). “Macromolecular crowding: obvious but underappreciated”. Trends Biochem. Sci. 26 (10): 597–604. doi:10.1016/S0968-0004(01)01938-7
[16] Kopelman R (1988). “Fractal Reaction Kinetics”. Science 241 (4873): 1620–26. doi:10.1126/science.241.4873.1620
[17]http://www.edt-enzymes.com/howenzymesareproduced.html
[18] http://www.anilbioplus.com/Manufacturing.aspx
[19] http://www.bio-pro.de/magazin/thema/05073/index.html?lang=en&artikelid=/artikel/02777/index.html
[20] W. D. Schindler and P. J. Hauser Chemical finishing of textiles, The Textile Institute, Woodhead publishing Ltd., Cambridge, 2004