Part 1 examined the environmental impact of the textile industry, highlighting the rise of synthetic fibers and fast fashion as key drivers. It reviewed EU policy initiatives focused on enforcing sustainable practices, the concept of a circular economy, and the early efforts and challenges in industrializing textile recycling. Part 2 delves into the technical challenges involved.
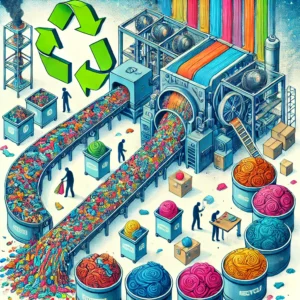
The complexity of textile recycling stems from the diverse mix of fibers with unknown origins and varying chemical compositions (Table 1). Each fiber type has its own ideal recycling process (Table 2), and blends are particularly challenging because they require separation into their individual components. Additionally, colorants and chemicals from processing and finishing must be removed, further increasing the complexity. Comprehensive reviews have summarized the current state of research and industrial activities in this area [1, 2].
Proper sorting of textile waste is the crucial first step, aided by automated detection of fiber materials using infrared (IRS) and near-infrared spectroscopy (NIRS). Automated sorting is considered faster and more reliable than manual methods.
Technical Challenges in Textile Recycling
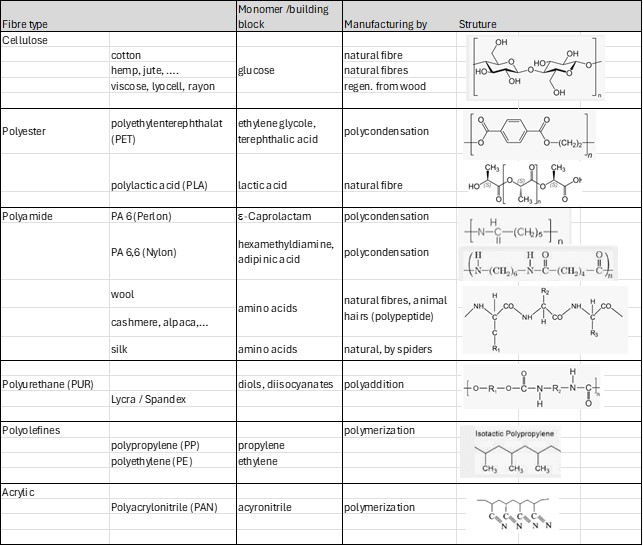
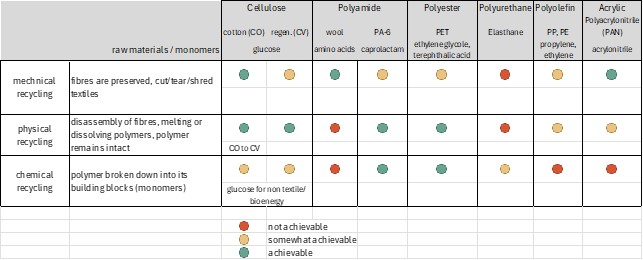
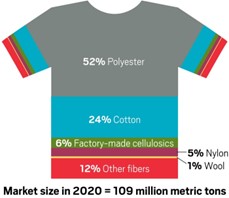
Polyester and cotton, the most widely used materials in textiles, together make up 80% of the market (Fig. 4), with polyester alone accounting for 52%. Consequently, most R&D and pilot activities have focused on these materials.
Recycling polyester (PET) from bottles into textile fibers is already well-established. This process involves physically recycling the polymer fibers, which results in a loss of quality and altered properties, such as in coloration. However, recycling textile waste is more complex due to contaminants, dyes, and chemicals that must be removed. Therefore, chemical recycling, which breaks the polymer down into its monomers for re-polymerization, is more appropriate than physical recycling, where the polymer backbone is retained.
Decolouration of Textile Waste Material
For PET, primarily disperse dyes are used, which can be removed through solvent extraction using dipolar aprotic solvents such as DMF (N,N-Dimethylformamide [1]) or DMI (1,3-dimethyl-2-imidazolidinone [3]). It’s crucial that these solvents are also recycled to ensure the process remains sustainable and circular.
For cellulose, the situation is more complex than with polyester, as it involves various dye classes (e.g., reactive, direct, vat, or sulfur dyes). A significant challenge arises from dyes and chemicals that form covalent bonds with the fibers, particularly reactive dyes and some finishing chemicals. The depth of the shade further complicates dye removal. While some dyes can be stripped using caustic soda and additional chemicals, not all dyes are easily removable.
In future classifications, “recyclability” could be a key criterion for labeling dyes. For instance, reactive dyes with vinylsulphone anchors can be stripped in the presence of strong alkali, breaking the dye-fiber bonds, whereas heterocyclic reactive dyes are not as easily removed. Bleaching with strong reducing agents can destroy many dyes, but the remaining fragments may affect the fiber’s properties in subsequent processes. Although chemists at dye manufacturers might know which dyes are recyclable, textile waste is often a mix of unknown compositions, making analysis complex. Improved traceability in the future could assist in sorting textile waste for optimal dye removal, leading to more efficient recycling processes.
Remaking Textile Fibers from Decolorized Textile Waste
After decolorization and cleaning, additional processing steps are required to remake fibers (Fig. 5). In chemical recycling, decolorized PET polymer is broken down into its monomers, terephthalic acid and ethylene glycol, through hydrolysis. These monomers are then used to produce new PET fibers with properties identical to virgin PET.
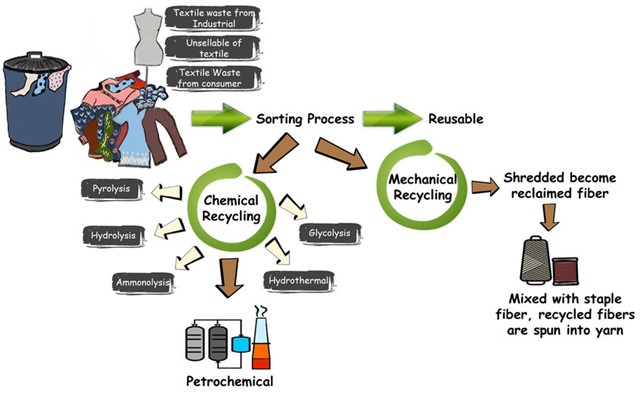
Polyamide is another fiber of interest. BASF, for instance, has developed loopamid®, which is made from textile waste degraded into caprolactam, the building block of polyamide 6, allowing for the regeneration of polyamide 6 fibers with original quality. Fishing nets collected from oceans are also a potential source of polyamide.
For cotton, although it can be degraded into glucose units using enzymes or acid, there is currently no industrial process to reconstruct cellulose from glucose. Instead, cotton recycling involves dissolving the cotton in appropriate solvents to produce regenerated cellulose fibers. NMMO (N-methyl-morpholine-N-oxide), used in the Lyocell process, is one such solvent, and cotton waste can serve as an alternative raw material. Lenzing’s Refibra® technology operates on this principle. Other solvents include ionic liquids [4] , ionic liquids [5] and deep eutectic solvents [6], which are being explored in new scientific approaches. As with other processes, the solvents used to dissolve fibers must be recycled to ensure sustainability and circularity. Ideally, these solvents should be non-toxic and non-hazardous, considering potential losses during the recycling cycles.
For polycotton, a blend of cotton and polyester, the waste streams must be separated into cellulose-rich and polyester-rich fractions. Each stream is then treated with appropriate methods (Fig. 6). Cellulose can be separated by dissolving it with suitable solvents, as mentioned earlier. Polyester can be separated through hydrolysis into ethylene glycol and terephthalic acid or through glycolysis into BHET (Bis(hydroxyethyl) terephthalate), an alternative raw material for making PET. Alternatively, PET can be dissolved in DMSO (Dimethyl sulfoxide).
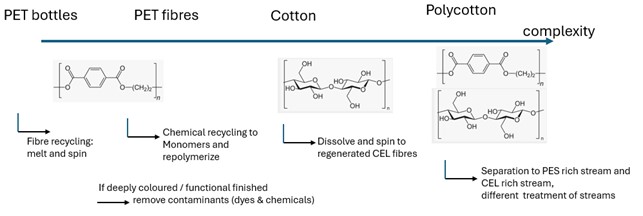
Worn Again, a UK-based pioneer in this field, has partnered with Oerlikon, Sulzer, H&M, and others to build a state-of-the-art textile recycling facility in Winterthur, Switzerland.
Conclusions and Outlook
The textile industry is entering a significant transition from being a highly resource-intensive, polluting, and waste-generating sector to adopting a circular and sustainable model. This shift will be long and challenging. From a purely economic and competitive standpoint, the ramp-up phase may not be viable without substantial investment and commitment from various stakeholders, including brands, mills, machinery manufacturers, and chemical suppliers. Consumers will also need to change their habits—fast fashion must decline, and there will be a need to embrace recycled textiles at higher prices. McKinsey’s analysis suggests that a 25% increase in fiber costs would result in only a 3% increase in retail prices, implying room for more expensive recycled fibers; however, the feasibility of this assumption remains to be seen.
European policies will drive this transition, making it inevitable. Starting from less than 1% closed-loop recycling, the industry has a long way to go, but significant growth is expected in the coming decades. We hope that Europe won’t stand alone in this effort and that industry commitments will extend beyond mere greenwashing during this crucial transition.
References:
1. Wang,S., Salmon,S., Sustain. Chem. 3 (2022), 376, “Progress toward Circularity of Polyester and Cotton Textiles”
2. Harmsen,P., Scheffer,M., Bos,H., Sustainability 13 (2021), 9714, “Textiles for Circular Fashion – The Logic behind Recycling Options”
3. Patent application WO2016/012755 (Walker,A., Worn Again, 2014)
4. Morais,S., et al., Molecules 2020, 25(16), 3652, “Use of ionic liquids and deep eutectic solvents in polysaccharides dissolution and extraction processes towards sustainable biomass valorization”
5. Dissanayake,N. et al. Carbohydrate Polymers 221 (2019) 63
6. Ismat Ara, Lahti University of Technology, Master thesis (2023), “recycling of waste blended textile with green solvent and close the loop”