Jeans bleaching – advantages and risks of different bleaching processes (2/3)
In the first part of the jeans bleaching report a general overview was given on the sequence of wet garment processing, and in particular, on the special requirements of the denim bleaching process.
In this part an overview is given on the different bleaching processes, their benefits and features, but also the problems of the various treatments. Most bleaching processes are made on open-pocket washing machines or barrel machines (sometimes in Asia), in which many denim products can be treated together. The difference between these machine types is the diameter of the drum and the speed of rotation. The recipes and running times in this report are based on recipes for open-pocket machines. But there are also some mechanical and technical treatments, which are carried out for each single garment.
1) Bleaching with sodium hypochlorite is by far the most common bleaching process. It is used when the indigo’s color needs to be lightened as required by fashion, as well as clean up the pocket linen and the inner face of the jeans (weft). This particular bleaching process is preferably used whenever a strong contrast between blue and white fibers is desired, since it gives the bluest cast of all bleaching processes. Moreover, this process is very cost-effective, however, a major disadvantage is that the AOX content, a measure of organic halogen compounds, often exceeds the permitted effluent pollution.
Sodium hypochlorite is a powerful oxidizing agent with a corresponding high redox potential. Hypochlorite consequently reacts relatively unselective, it reacts even with the fibers. The danger of fiber damage with this bleaching agent is much greater compared to other bleaching processes. Due to its high oxidation agent potential, hypochlorite bleaching is carried out at low temperatures (approx. 40 °C). [1]
The actual bleaching agent in bleaching liquors is not sodium hypochlorite (NaOCl) itself, but the hypochlorous acid (HOCl) which is formed from it in a pH sensitive equilibrium. In order to ensure mild bleaching conditions, a pH range between 9.0-11.5 has been found as optimum range for effective bleaching. Since, under practical conditions, pH levels below 10 are difficult to keep constant, an initial pH range between 11.0-12.5 is selected, as a rule to take into account the consumption of soda ash or caustic soda.
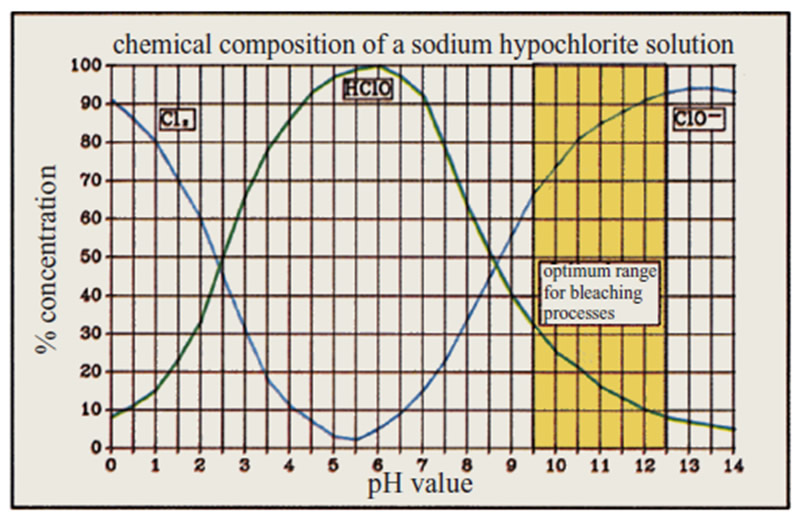
The control of the pH value is very important. The strongest bleaching activity is at pH 9.5 – 12.5; at pH 5 – 7 the activity is the lowest.[2]
After reaching the required bleaching effect, the bleaching process has to be stopped in the same bath by using hydrogen peroxide or sodium bisulfite.
Another disadvantage of hypochlorite is that the solution loses strength over time, especially at higher temperatures in hot regions. This makes the reproducibility much more complicated, because the amount of hypochlorite should be adjusted by the strength of the solution. But mostly it is only adjusted by continuously checking the bleaching progress.
Comparison of the steps untreated, stone wash and peroxide bleaching
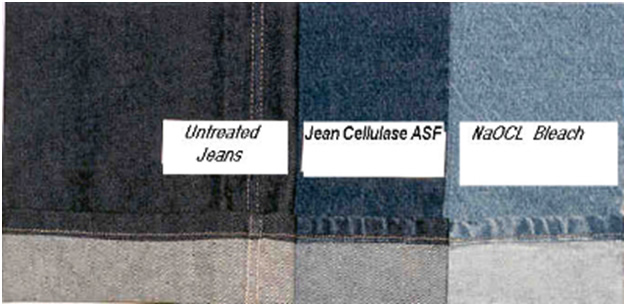
2) Bleaching with potassium permanganate
Potassium permanganate is a very strong oxidative agent. It’s a deep red-violet metallic shiny crystalline solid. It can be dissolved in water to form a dark violet solution which is well suitable to bleach denim. Potassium permanganate can be used for local bleachings by spraying application or for complete treatments in drum washing machines. The potassium permanganate solution must be mixed very well with the washing liquor, because undissolved permanganate can cause different shades in only one bath.
In contact with the jeans active oxygen is formed in the following reaction:
2 KMnO4 + 3 H2O ———> 2 KOH + 2 MnO(OH)2 + 3/2 O2
After reaching the desired bleaching effect the rest of unconsumed potassium permanganate and the formed brown manganese oxide hydrate have to be removed thoroughly. After 1-2 rinse bathes the removal of the remaining manganese oxide, is usually carried out with sodium bisulfate, respectively SO2.[2]
MnO(OH)2 + SO2 ———> MnSO4 + H2O
This bleaching process can be used even for very pale shades, because potassium permanganate can reduce indigo as well as sulphur dyes. When a longer bleaching process is applied, the jeans processed accordingly can even be completely decolorized.
The reproducibility of the bleaching effect is very good, as long as the same conditions are kept in terms of load weight, liquor ratio, temperature, run time, pH and amount of potassium permanganate. The fabric is not as stressed as with hypochlorite. However, the blue cast is very grey and the garments become very flat.
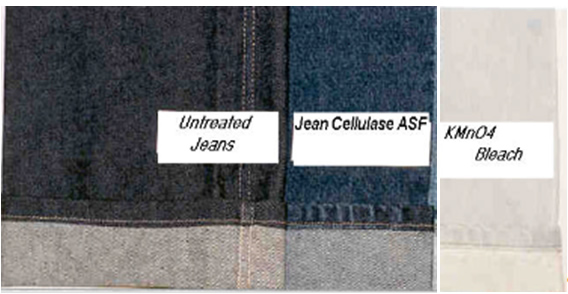
3) Hydrogen peroxide bleaching has gained in importance in view of the effluent problems caused by hypochlorite bleaching. Hydrogen peroxide is a chemical compound, which reacts as and oxidizing agent. Bleaching with hydrogen peroxide is typically chosen for denim articles whenever a high whiteness is requested. But also black denims are usually bleached with hydrogen peroxide, because it avoids a yellowish tone, as it is obtained in case of hypochlorite bleaching [1].
Hydrogen peroxide dissociates only slightly in an aqueous medium. The free acid has only a very weak bleaching action:
For this reason, hydrogen peroxide bleaching is carried out exclusively in alkaline medium. If the hydrogen peroxide solution is activated with alkali, then the dissociation equilibrium is moved to the right and the concentration of perhydroxy anions is increased:
For cotton fibers caustic alkaline bleaching liquor is preferred. In addition to the bleaching chemical H2O2 and the alkali as activator, the bleaching formulation basically also contains a scouring and wetting agent for improving the liquor penetration. Stabilization of the hydrogen peroxide is of fundamental importance to achieve a uniform bleaching effect. Moreover, for bleaching in hard water the use of a complexing agent is required. Otherwise catalytic damages may cause small holes in the garment (especially in knit wear)[2].
The bleaching process can be stopped by 1-2 rinse baths and a neutralization of the alkali process with acetic acid. But residues of peroxide can cause catalytic damages. By using catalase the processor is on the safe side. Catalase is a common enzyme, which catalyzes the decomposition of two molecules of hydrogen peroxide to water and oxygen.
4) Bleaching with Organic Peroxide
The bleaching with organic peroxide is comparable to bleaching with hydrogen peroxide. Both are compounds of the peroxide family. The bonding between the both oxygen atoms is very instable and can be easily split at mild conditions. One of the most important organic peroxides in terms of applications is dibenzoyl peroxide [3]
In the textile industry this product is used in lower concentrations (approx. 20-30% in mixtures). Benzoyl peroxide is a very aggressive and corrosive product. The most common mixtures are based on inert material like calcium chloride.
In the jeans bleaching has the product very versatile and dynamic properties. On different material it can have different effects. It is therefore not possible to give standard recommendations. The bleaching effect increases proportionally to the amount of organic peroxide. But this product can also be used for Jeans containing elastic fibers. The bleaching effect can be stopped by adding caustic soda to the bleaching bath. Blue denims get after the bleaching a grey cast.
5) Bleaching with Laccase
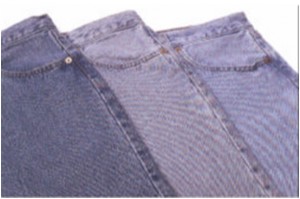
Laccase are useful enzymes for industrial applications. They would be used in the beginning for the waste water treatment. The advantage of enzyme products is the specific treatment. This product preferentially breaks down the indigo molecule, without affecting sulphur, reactive or direct dyes. This process is not useful, if the fabric contains special bottomings or toppings which are typically made with said other dyestuff classes.
There is a tendency to have a grayish or antique shade, as opposed to the light blue cast normally associated with sodium hypochlorite bleaching.
Laccase does not affect harmfully on the strength of the fabric and is also suitable for denim containing elastic yarns. It also does not damage leather labels or metal trims.
Laccases have relative low redox potential, which can be increased though a mediator-involved reaction mechanism. Redox mediator’s low-molecular weight compounds that are easily oxidized by laccases producing: [4]
The figure shows a schematic representation of laccase catalyzed redox cycles for substrate oxidation in the absence (A) or in the presents (B) of redox meditators [4].

A laccase-mediator-system (LMS) has been introduced in the textile industry for Indigo oxidation of denim garments in drum washing machines. The indigo dye chromophore is split to yield two molecules of uncolored compounds (isatin).
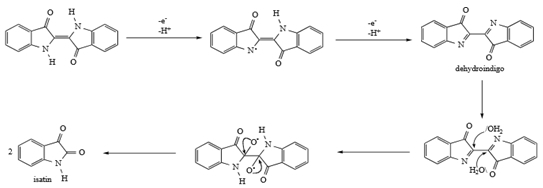
6) Bleaching with Ozone
Ozone is a very reactive gas which can easily release one of his three oxygen atoms for further reactions. This free and high reactive oxygen atom bleaches the indigo molecule. Usually a generator is needed to produce ozone gas from compressed air. This gas needs to be injected into a washing machine loaded with jeans. The garment can be wet or dry. If the fabric is wet the bleaching effect is stronger and faster. The obtained color cast is also a bit greyish than bleached with hypochlorite.
The glucose bleaching process is a reductive bleaching. This bleaching process is an inverse dyeing process with glucose as reducing agent. Glucose converts at strong alkaline pH values and temperatures of at least 80 °C (mostly carried out at 90–95 °C) the indigo pigment into the water soluble leuco indigo, which can strip easily from the fiber. In the bleaching bath a strong dispersing agent is needed, so that the leuco indigo does not dye the white weft yarn. Due to the oxygen in the drum washing machine the soluble leuco form converts back to the insoluble indigo pigment. This pigment form is drained with the bleaching bath, followed by 1-2 rinse bathes.
The bleaching process with glucose was promoted for long time as the preferred ecological form of bleaching, however, this process requires much energy due to high temperature, and the waste water has a high pH value and a very high COD load.
8) Sandblasting is a mechanical method to lighten Jeans. In this process the sand is blown with high pressure to the surface until the blue shade gets lighter and the vintage look arise. The abrasion on the surface gives a look “like used yet”. Starting end of the 90ies the vintage look has been a high fashion look with a great demand.
The biggest problems of the sandblasting process with high pressure are the working conditions. Most workers do not wear neither protective masks nor workwear. Due to the high pressure quartzous dust particles are formed. If this mineral gets in the lung, composite nettings results in cicatrization of the lung. At the end the worker suffers from silicosis, which is known in the metal and mining industry. [8],[9]
Since 2008 several media published reports about the sandblasting process and the problem of workers affected by silicosis. The campaign “Clean Clothings” and the Swede Fair Trade Center tried to convince the brands to abstain from the sandblasting for jeans treatment[13]. In the the meantime most jeans brands have put sandblasting on their restricted lists. Turkey has restricted the use of sandblasting in 2009, but mostly this treatment is used in countries like Pakistan, China, Bangladesh and Egypt. In particular, sandblasting is used for plagiarism of the big brands [8].
Here is a video of Sandblasting with English subtites (17.02.11)[10]:
9) Electrochemical Bleaching
Electrochemical procedures are methods, in which electrons are transferred between chemicals via electrodes through electrical currents. In the production of reduction and oxidation agents electrochemical processes are well known, and frequently used in the production of various raw materials. But as of today they are not yet used in jeans bleaching process.
The electrochemical bleaching system (ECB) of indigo dyed jeans garments was developed at the institute for Textile Chemistry and Textile Physics, Dornbirn, based on former studies in the institute about the waste water decoloration with an electrochemical treatment. Based on the comparison with other bleaching systems, it was shown that the total eco balance of the production of blue jeans based on pre-reduced indigo, and using the electrochemical bleaching process, is the optimum. [11]
The ECB has economic and ecological advantages against the other bleaching processes. The process is easy to carry out, well repeatable, cost-saving and possibly with low waste water.
ECB can be used for oxidative or reductive processes. In both processes a mediator is needed – like in the laccase process.
In the oxidative ECB process the mediator is oxidized at the anode. The activated mediator oxidizes the water-insoluble indigo on the fabric surface to a water soluble decomposition product. The movement in the washing machine remove the decomposition product from the surface and a dispersing agent hold it the bleaching bath. The principal of the oxidative ECB process is shown as follows :
If sodium chlorite is used as mediator, it is converted in the process to hypochlorite. The bleaching reaction is the same like in the standard hypochlorite bleaching process. In opposite to the standard process the regeneration of the bleaching agent is at the cathode. [12]
Anodic reaction:
Cl– + H2O OCl– + 2e– +2 H+
Cathodic reaction:
2 H2O + 2 e– H2 +2OH–
In the reductive ECB process the washing machine must be free of atmospheric oxygen, because in this process the mediator is reduced at the cathode. When there is oxygen in the in the washing machine the reaction is reduced or blocked.
The mediator takes electrons from the cathode and is converted to the reduced form (1). The reduced mediator transfers the electrons to the oxidized, water-insoluble dyestuff on the fabric surface (2). Thus the dyestuff is reduced and water-soluble (3). The movement in the washing machine removes the water-soluble dyestuff from the surface (4) and a dispersing agent holds it the bleaching bath (5). The oxidized mediator is subsequently reduced at the cathode again (6) [11].
10) Laser Engraving
The laser burns the surface of the denim fabric. Depend on the intensity of the laser every color from blue to complete white can be achieved. As lighter the bleaching effect is, as higher is the fiber damage, which can cause breaking of the fabric.
The laser treatment can imitate all different washing effects without any chemicals a specialty of the laser is the burning of special “tattoos” on the fabric. So it is possible to make headlines on the legs or make special pictures on the jeans. The laser engraving process is a discontinuous process, a process in which each jeans is produced one after another. But the treatment of one jeans requires only – depending on the effect – a few seconds.
The lasers are in general automatic machines. The laser system has a built-in vent that sucks up the dust before they disperse into the air. The technology of the most machines is so safe, that face masks are only optional.
Outlook
In the following and last part the different jeans bleaching treatments are compared in a summary to illustrate their advantages and disadvantages. The use of chemicals will be assessed opposite the targets of the big brands´ ZDHC project, to find processes with lowest impact to the environment. Ultimately meeting the target is to select processes which have a good price/performance level, good reproducibility and use environmental friendly materials.
[1] H.K. Rouette “Encyclopedia of Textile Finishing“, Springer-Verlag Berlin Heidelberg New York, ISBN 6-84569-065-6, 2002
[2] M.Peter, H.K. Rouette “Grundlagen der Textilveredlung”, Deutscher Fachverlag, ISBN 3-87150-277-4, 1989
[4] S. Riva, “Laccases: blue enzymes for green chemistry”, Trends Biotechnolgy, vol. 24, pp 219-226, 2006
[5] M.R. Hu, Y.P. Chao, G.Q. Zhang, Z.Q. Xue, S. Qian “Laccase mediator system in the decolorization of different types oof recalcitrant dyes”, J.Ind. Microbiol. Biotechnol., Vol 36, pp. 45-51, 2009
[6] R. Campos, A. Kandelbauer, K.H. Robra, A. Cavaco-Paulo, G.M. Gübitz, „Indigo degration with purified laccases“, J. Biotechnol., vol. 89, pp. 131-139, 2001
[8] Spiegel-online, “ Türkische Textilfabriken: tödlicher Sand in der Jeans-Maschine, 22.03.2008“, EvB „Sandstrahlen mit tödlichen Folgen“
[9] Die Welt “‘Killer-Jeans‘ kosten Sandstrahlarbeiten das Leben”, 30.11.2010
[10] http://www.youtube.com/watch?v=Jrt4UKxxq6k 17.02.2011
[11] W. Schrott, “Sustainable Denim – Eco-Labeling and Enviromental Friendly Denim Production“, University of Applied Sience, Hof, 15.08.2011
Patent « Process for reducing dyes », 01.06.1989, WO1990015182A1
[12] P. Maier, W. Schrott, T. Bechthold, R. Campese, “Electrochemisches Bleichen in der Veredlung von Jeans”, MTB, Vol. 85, pp. 880-884, 2004
Patent „Method for modification the color of dyed textile substrates” 13.12.91, WO2003054289A2
[13] Medicus mundi Schweiz “Clean Cloth Campaign fordert den Stopp sandgestrahlter Jeans”