After introduction in part 1, part 2 will look deeper into some of these applications of ionic liquids for the textile industry.
Ionic liquids in textile fibre manufacturing
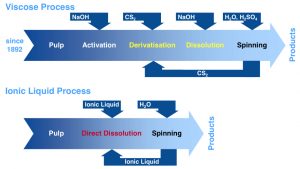
Many approaches for use of ionic liquids in fibre manufacturing have been examined in the last 15 years1. Most notably, research was conducted in cooperation with the Institut für Textilchemie und Chemiefasern (ITCF), Denkendorf and the Thüringisches Institut für Textil‐ und Kunststoff‐Forschung (TITK), Rudolstadt, and the chemical company BASF2. The Figure shown here illustrates the potential advantages of a ionic liquid process compared with the conventional viscose process. The ionic liquid process is shorter and is environmentally favorable. The conventional viscose manufacture involves hazardous chemicals like CS2 and causes heavy pollution due to H2S, SO2, and sulfuric acid. The new ionic liquid process would be also in competition with the process used for Lyocell fibres (brand name: Tencel), made by Lenzing since the 1990. For Lyocell, the solvent N-Methylmorpholin-N-Oxid (NMMO) is used. Selected ionic liquids are non toxic and chemically as well as physically neutral – an advantage compared to NMMO used in Lyocell. Fibres can easily be prepared by coagulation in water and subsequent spinning processes.
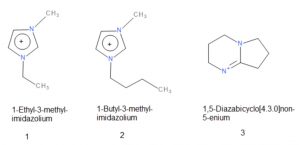
In the trials carried out at ITCF Denkendorf, Cellulose is dissolved in the ionic liquid 1-ethyl-3-methylimidazolium acetate, and after wet spinning a regenerated cellulose fibre was produced on pilot plant scale. The fibre showed higher tenacities than those produced by conventional wet spinning.
The ionic liquid 1,5-diazabicyclo[4.3.0]non-5-enium acetate (Figure 2, structure 3, abbreviated “[DBNH] Ac“), was identified as an excellent solvent for cellulose fibre spinning, avoiding the otherwise extensive fibre degradation, and intensively studied in Finland3.
Ionic liquids for recycling of textiles
Since certain ionic liquids are able to dissolve textile fibers, there is a potential of applications in the recycling of textiles as well.
As mentioned, the ionic liquid [DBNH] Ac was found suitable to dissolve cotton. It is claimed that a new process based upon [DBNH] Ac „allows the production of virgin textile fibers of substantially higher quality than that from the mechanical recycling methods that are used currently“4. [DBNH] Ac is a distillable liquid with promising properties for recycling technologies5.
Excellent review article by Chinese authors6 highlights recent advances in the field of dissolution and processing of cellulose with ionic liquids.
„Trash-2-Cash“7, a EU funded research project, covers recycling strategies for cotton and polyester-based waste textiles, aimed at „new fibres from pre-consumer and post-consumer waste“. Cotton/polyester blends are a challenge for recycling. Once the cotton was separated from the polyester, it could then be spun into fibers — thereby becoming the basis for new materials.
Ionic liquids in coloration, used as dyeing medium
A high consumption of water, energy and chemicals is required for coloration of textile fibers. In particular, the dyeing of PET (polyethylenterephthalate) polyester fibers with disperse dyes requires high processing temperatures of 130 °C or more, in closed dyeing machines operating under pressure.
A potentially revolutionary approach applies ionic liquid as a dyeing medium, and being recycle-able totally substitute water form the dyeing process. This research, carried out at Deutsches Textilforschungszentrum Nord-West (DTNW) in Krefeld,Germany, has shown that certain ionic liquids are suitable as dyeing medium for textiles (e.g. for disperse dyes, cationic dyes, reactive as well as metal complex dyes). DTNW, who was already a pioneer in the development of dyeing from supercritical CO2, has examined a technique to dye various fibres in ionic liquids, and investigated for the commercially most important fibre PET. In a recent paper, the DTNW scientists claim to perform „a pressure-free dyeing at high temperatures with minimal air pollution“, enabling „the textile industry in future to carry out their business with new methods avoiding high consumption of energy, water and chemicals“8.
Promising results were obtained by using 1-ethyl-3-methyl-imodazolium methyl sulfate (Figure 2, structure 1). Acceptable color fastnesses were obtained. The ionic liquid solvents could be reused for at least 10 cycles.
Polyester/cotton blends in one step dyeing was also examined in the same paper.
In a collaboration, DTNW and Centexbel, a collective research networking project was initiated to investigate further this novel approach of textile dyeing in ionic liquids9.
The coloration of cotton is highly water consuming. To address this issue, a dyeing process with only two dyeing agents, a reactive dye and a ionic liquid as dyeing solvents was investigated by Brazilian scientists10. The authors claim that after dyeing the unfixed dye would remain active in the bath, in contrast to conventional dyeing processes.
Ionic liquids in coloration, used as dye bath additive
A Chinese patent of Qingdao University11 claims the use of a quaternary ammonium ionic liquid used as auxiliary in the dyebath for the dyeing of cotton with reactive dyes.
Italian researchers12 investigated the dyeing of wool, polyester, and cotton with a disperse dye using ionic liquid, 1-(2-hydroxyethyl)-3-methylimidazolium chloride, used as additive to the dyebath in isothermal dyeing at 95 °C, applied for polyester and wool in an open vessel and without using additional dye bath additives. The authors claim „outstanding effects“ in the coloration of „several kinds of fibers (cotton, wool, and polyester) employing exclusively three components: pure disperse dye, water, and an appropriate ionic liquid.“
Further applications of Ionic liquids
The application of ionic liquids in textile wastewater treatment by liquid-liquid extractions is another topic of particular research activities. The removal of various dyestuff classes, acid dyes, basic dyes, vat dyes (indigo), direct dyes and reactive dyes were examined in scientific studies1.
Many potential applications are conceivable in finishing applications. Antimicrobial finishing on wool13, antifungal finishing, UV-protection, flame-retardant finishing, water-repellency and comfort finishing are among the published research activities1.
It is beyond the scope of this short article to discuss further potential applications in detail. Literature sources can be found in the review article of Meksi & Moussa1.
Conclusions
Ionic liquids have potentially outstanding potential in the textile industry and beyond. Some of the potential areas of applications are briefly outlined above.
Although there is notable progress in fundamental research, the technology is still largely in R&D stage. The question comes up why are ionic liquids not yet applied in the textile industry? Generally, there are still certain limitations which have slowed down or prevented further industrial use.
First of all, the textile industry is very cost conscious and the cost of ionic liquid chemicals is comparably high. Therefore, it is essential to use efficient recycling technologies for multiple reuse of the ionic liquid, without decrease of performances and no significant losses. For commercialization we need to solve the recycling issue of the ionic liquid. These technologies require capital expenditure for investments.
Secondly, there are still technical challenges to overcome. The high viscosity of ionic liquids, comparable of oil, is a technical challenge for many applications that needs to be overcome.
Thirdly, although ionic liquids are thought to be less hazardous and toxic due to their low vapor pressure, no profound knowledge yet about biodegradability and toxicity is available.
Many ambitious claims have been made so far, but most of the time the proof of concept is missing.
Nevertheless, ionic liquid are an exiting topic worth to be pursued further beyond research stage.
A compressed version of this article (all parts) was published in the journal International Dyer & Textile Finisher 5/2018, 21-25.
References
1. Meksi, N., Moussa,A., „A review in the progresss in the ecological application of ionic liquids in textile processes“, J. Clean. Prod. 161 (2017), 105-126
2. Hermanutz, F. et al., „Special Issue: Structure and Properties of Cellulose: New Developments in Dissolving and Processing of Cellulose in Ionic Liquids“, Macromol. Symp. 262 (2008), 23-27
3. Hummel M. et al. , „Ionic Liquids for the Production of Man-Made Cellulosic Fibers: Opportunities and Challenges.” in: Rojas O. (eds) Cellulose Chemistry and Properties: Fibers, Nanocelluloses and Advanced Materials. Advances in Polymer Science, vol 271 (2015). Springer, Cham
4. Asaadi,S. et al. „Renewable High-Performance Fibers from the Chemical Recycling of Cotton Waste Utilizing an Ionic Liquid“, ChemSusChem. 9/22 (2016), 3250-3258
5. Parviainen,A. et al. „Sustainability of cellulose dissolution and regeneration in 1,5-diazabicyclo[4.3.0] non-5-enium acetate: a batch simulation of the IONCELL-F process“, RSC Adv., 2015, 5, 69728-69737
6. Zhang, J. et al., „Application of ionic liquids for dissolving cellulose and fabricating cellulose-based materials: state of the art and future trends“, Mater. Chem. Front., 2017,1, 1273-1290
8 Opwis, K., Benken, R., Knittel, D., Gutmann, J. „Dyeing of PET Fibers in Ionic Liquids“, International Journal of New Technology and Research 3/11 (2017), 101-108
10. Andrade, R.S. et al., „Sustainable Cotton Dyeing in Nonaqueous Medium Applying Protic Ionic Liquids“, ACS Sustainable Chem. Eng., 2017, 5 (10), pp 8756–8765
11. Qingdao University, Chinese patent 102493222 A
12. Bianchini, R., et al. , „Ionic Liquids Can Significantly Improve Textile Dyeing: An Innovative Application Assuring Economic and Environmental Benefits“, ACS Sustainable Chem. Eng., 3/9 (2015), 2303–2308
13. Kantouch,A. et al. „Antimicrobial finishing of wool fabric using ionic liquids“, The Journal of The Textile Institute 104 /4 (2013), 363-369