Dyeing with supercritical CO2 – finally a success story?
Summary
Dyeing in supercritical CO2 could finally be on track for success after 25 years of development. Originally an idea of German universities, it was developed and brought to market by the Dutch start-up company DyeCoo. I have already covered the same story in 2012.
With this innovative, environmentally friendly and water-free dyeing technology, today sportswear textiles made of polyester are produced in Asia for the brands of adidas and Nike. Carbon dioxide (CO2) turns to a supercritical state at a pressure higher than 73.8 bar and a temperature higher than 31.1 ° C (Figure 1). Supercritical is a condition with high solvency power and excellent permeability. The use of supercritical carbon dioxide (hereinafter abbreviated as “scf-CO2“, said scf stands for “supercritical fluid”) in extraction methods is known for a long time, e.g. for the extraction of caffeine from coffee. The concept of dyeing from scf-CO2 has long been on everyone’s lips in the industry as well as in academia.

History of the scf-CO2 dyeing technology
The scf-CO2 dyeing technology has been developed since the late 1980s at German universities by the pioneering work of Eckhard Schollmeyer and co-workers, involving several industrial partners in the pilot stage [1]. In the mid-1990s the German companies Jasper and Uhde Hochdrucktechnologie built and installed pilot plants in the textile industry, for example at Amman und Söhne [1] in Germany. However, at that time the technology failed to commercialize.
Almost two decades later a production machine was designed and built by the Dutch start-up company DyeCoo Textile Systems BV. For several years, these dyeing machines have operated in Thailand and Taiwan with very good results.
How was that possible? Why failed in Germany which has been successfully implemented elsewhere? There are various reasons for this: Back in the 1990’s, the high capital costs for supercritical CO2 production machines were prohibitive. The time was not yet ready to fully appreciate the value of this technology.
Reasons for the success of the scf-CO2 dyeing
The key reasons for the success in the 2010s were a changed market environment and increased awareness for the environment, in particular for the significance of the factor water. In the 1990s environmental requirements had been an issue mainly in Central Europe. However, the textile industry could avoid the environmental and cost pressures imposed by retailers: They shifted production to Asia. Today the situation has changed. The Asian textile producers also feel the pressure to become more sustainable, not only because of the environment: since labour costs are much lower in Asia, the relative share of water in the operating costs there is significantly higher than in Europe.
Water scarcity is an issue in major regions where textile production takes place today, particularly in India (Tamil Nadu, Punjab), Pakistan and in northern China [2]. According to the Water Footprint Network 4 billion people worldwide will be affected by water scarcity [3]. The so-called “Grey Water Footprint”, water contamination caused by industrial processes [4], is particularly critical in many key regions of the manufacturing textile industry. Here, dyeing processes plays a major role. For example, a detailed study of Fountain Set in China illustrates the same [5]. Today, recycling technologies caused by the lack of water, are common practice in important textile regions of South India.
Greenpeace has launched its Detox campaign [6] wherein the subject of clean water in the textile industry is in focus. They put strong pressure on the textile industry and the textile supply chain of retailers in recent years. In this environment the project of waterless dyeing using supercritical CO2 came just right: for that you don´t need any water and there is virtually no waste – 95% of the materials can be recovered through recycling.
By using scf-CO2 colouration can be done even regardless of the availability of water: “You can dye fabric in the middle of the Sahara”, is one of the messages on the website of the machine builder DyeCoo.
But ultimately the most important factor for a successful commercial implementation was finally the support of global players such as Nike and adidas, who have discovered the subject of water for their sustainability agenda.
Development of the technology to market scale
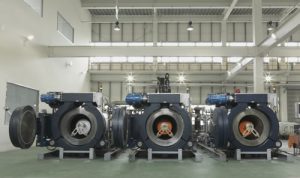
The basic patents of Schollmeyer et al. [7] have been abandoned or expired, at the time when DyeCoo was founded, around 2008. Geert Woerlee, founder of the technology company Feyecon, is the man behind DyeCoo. He brought the technology to market at the end of the 2000s with entrepreneurial spirit and support from the University of Delft (Netherlands). Feyecon founded the start-up company DyeCoo and succeeded in attracting a leading textile group as an investor: The Yeh Group. Today DyeCoo´s scf-CO2 production dyeing machines (Figure 2) run at two textile producers: in Thailand at Tong Siang (part of Yeh Group) and in Taiwan at Far Eastern New Century Corp. Both are dyeing 100% polyester (polyethylene terephthalate – PET) at a pressure of 250 bar and a temperature of 120 °C. The dyeing machine called DyeOx has a daily capacity of 4 tons, with 20 to 200 kg of goods per batch in three separate chambers. It produces sportswear made of polyester for Nike and adidas, which are marketed under the brands DryDye (adidas) and ColourDry (Nike).
After years of practical use the feedback from the market is very positive: The dyeings are similar or better in terms of levelness and colour fastness compared to conventional aqueous dyeing, when the scf-CO2 colouration process is applied.
Dyes for scf-CO2 dyeing of polyester
Our long term customer Colourtex Industries Pte Ltd., a leading Indian chemical company based in Surat (Gujarat, India), manufactures and supplies the dyes [8]. Colourtex is the largest dye producer in India with a wide range of products, especially reactive, disperse and acid dyes. Colourtex is a long-term development partner of DyeCoo.
After the European dyes suppliers have downsized technical resources and closed various European R&D sites, it is only at first glance surprising that an Indian company is involved at the front of one of today´s most innovative dyeing technologies. But it should be mentioned that at least Huntsman Textile Effects, based in Singapore and Switzerland, is also a development partner of DyeCoo.
The dyes of Colourtex developed for the scf-CO2 dyeing process are marketed under the brand name ®Corangar. Corangar is a mixed word from the master brand (reactive dyes are called ®Corafix or ®Corazol, disperse dyes ®Coralene, etc.) and the Hindi word for carbon dioxide.
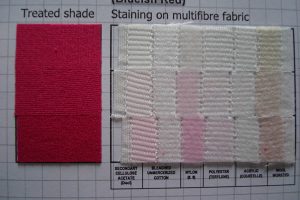
There currently are 21 Corangar PE dyes for polyester in the range. These are selected disperse dyes with a special finish. Not all conventional disperse dyes suitable for scf-CO2 dyeing, due to different, specific properties of the solvent scf-CO2 compared to water. Conventionally processed disperse dyes also contain large amounts of dispersing agents. Such dispersing agents are not necessary for scf-CO2 colouration. In addition, there is another advantage due to the non-usage of dispersing agents: no COD in the waste water. Due to the finish, dyeings with identical colorants are usually more brilliant as compared with conventional application in aqueous medium.
Remarkably, the washing and contact fastness properties by dyeing in scf-CO2 are in many cases superior to the fastness in conventional water dyeing. One can obtain significantly better fastness by the same underlying colorants; often one grade better in staining on adjacent fabrics [8]. Fig. 3 illustrates this effect with an example of a red disperse dyestuff.
For quality sportswear made of PET usually expensive, highly specialized disperse dyes, are applied in conventional aqueous process. In scf-CO2 less specialized colorants can be used to achieve acceptable washing and contact fastnesses for sportswear, even without reductive clearing!
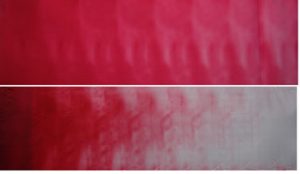
This may be surprising at first glance even for experienced dyestuff experts. However, the effect can understood and is explained like this: disperse dyes diffuse out of scf-CO2 faster into PET, compared to conventional aqueous method (Fig. 4). The detour via an aqueous dispersion of a molecule which is insoluble in water, so that it can migrate later into a hydrophobic PET matrix, cannot be optimal. Scf-CO2 is better: there is no need for a dispersion. The dyes dissolve directly in CO2 and diffuse more rapidly in the PET matrix. Faster diffusion means better migration and better dye penetration, which provides superior washing and contact fastness properties and the possibility of skipping the reductive clearing step. Abandoning the reductive clearing step also has the favourable consequence that no aromatic amines can be formed from azo dyes (which are the most commonly used type of dyestuffs). This avoids BOD / COD and is very beneficial for the environment.
Moreover, the exhaustion from the dye bath is faster and more uniform compared to aqueous dyeing (Fig. 5).
Possible application in other textile substrates
As stated, the scf-CO2 dyeing technology works very well for polyester. How is the situation for other textile substrates?
For polyamide a range acid dyes is at a late stage of development, and market launch can be so expected shortly. There are also promising solutions in the pipeline for elasthane fibres.
With respect to the application of natural fibres, the situation is not quite so rosy. What is the advantage with polyester – a hydrophobic fibre PET and water-insoluble disperse dyes fit well to CO2 – is a disadvantage of natural fibres like cotton. In cotton one deals with a hydrophilic fibre and water-soluble dyes, which is not a good fit at all for CO2. Colouration with the usual dyes – if possible at all – are rather superficial and have poor rubbing and wet fastnesses.
In particular, there is the problem of swelling of cotton. The existing hydrogen bonds have to be broken so that the fibre can swell and the dyestuff can penetrate into the pore structure of the cotton. Thermodynamically, the scf-CO2 dyeing process is problematic for cotton and therefore, there is no practical, commercially available solution for cotton in the market yet.
DyeCoo expressed optimism that solutions for wool and cotton would shortly be ready for the market [9]. As is known from the patent literature [1,10] swelling of the cotton fibre can be achieved by pre-treatment with hydroxy-groups-containing solvents (alcohols, glycols), or by using as co-solvent. Also, Feyecon holds a patent in this context [11]. But the use of solvents is not really a sustainable solution. One would have to wash out the solvent and dry the fabric. Such as process would also generate COD. The advantage of the waterless dyeing would be largely lost. Another conceivable interesting approach would be the use of reactive disperse dyes [12], which are today considered at research stage but not (yet) commercially available.
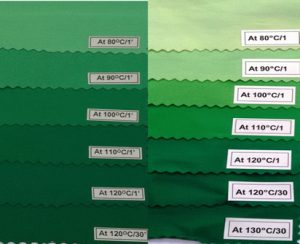
The lack of solution for cotton is regrettable, given the market significance of this fibre and the high water consumption in the conventional method of dyeing cotton. Also, cotton is – in contrast to polyester – a renewable fibre.
It would require new chemical approaches for cotton from research and development. European manufacturers have hesitated for a long time to enter the arena with new chemistry. The high development costs for a (still) small niche and the very complex, expensive registration under the EU chemical law REACh are in this case an obstacle to innovation. However, with the expected growth of the scf-CO2 technology this attitude could change. Today both production of dyes (India) and their application (Thailand, Taiwan) take place outside the REACh jurisdiction, in locations where new molecules can be used in production without legal restrictions. These new molecules could still be registered under REACh at a later stage, if necessary.
Outlook
In addition to the advantageous dyeing properties of scf-CO2, operating costs are significantly lower because of the dyeing process is only half as long as conventional. The energy consumption is reduced by 40%. The colour consistency in practice, is 98%.
So, only advantages? Now, of course, the scf-CO2 production machines are quite a significant investment and it takes time until such an investment shows a return on investment. Safety aspects at high pressures of 250 bar have to be observed as well. There are various security checks and loop backs built in, and the dyeing of DyeOx DyeCoo is certified by Bureau Veritas and Lloyds.
The dyeing technique of supercritical CO2 has been established successfully in recent years in practice. After the machine manufacturer DyeCoo presented its dyeing machine at the ITMA exhibition in 2015 in Milan, with a positive response to a wide audience, it can be expected that more textile dyehouses would acquire scf-CO2 dyeing machines. The rate-determining factor in the market currently seems to be how quickly the manufacturer can build and install their machines. Further expansion is expected in Italy, Turkey, South Korea and Vietnam, followed by USA, India and Japan [8].
The promoters and users are very optimistic [8]:
“We are aspiring to become the most eco-friendly textile group providing DryDye fabrics and garments”, stated David Yeh, Managing Director of Tong Siang Co. Ltd., and Mats Blacker, CEO of DyeCoo, is quoted saying „We see this as an important step towards revolutionizing the textile dyeing industry. This product line proves that our technology is economical viable and suitable to scale, while hugely decreasing environmental impact”
Currently, the scf-CO2 dyeing is running only with polyester (PET). Since polyester represents the largest and most important fibre class, this is for the further growth of the technology no real obstacle. This innovative technology of the scf-CO2 dyeing could therefore be a sustainable success, despite a long development time.
Remark:
A shorter version of this article was published by the author in German language in the journal textilplus in 5-6/2016.
Literature References:
- Bach, E., Cleveland, E., Schollmeyer, E., “Past, Present and Future of supercritical fluid dyeing technology – an overview”, Rev. Prog. Colour. 2002/32, 88-102
- Food & Agriculture Organisation of the United Nations: Water scarcity, Areas of water scarcity
- Mekonnen, M. M. and Hoekstra, A.Y., “Four trillion people facing severe water scarcity”, Science Advances, 2016/2 (2): e1500323
- Mekonnen, M. M. and Hoekstra, A.Y., “National water footprint accounts: the green, blue and gray water footprint of production and consumption”, Value of Water Research Report Series 2011/50, UNESCO-IHE, Delft, the Netherlands
- Wang, L .; Ding, X .; Wu, X., “Blue and gray water footprint of textile industry in China”, Journal of Scientific & Industrial Research, 2013/72, 710-715
- Greenpeace website
- Schollmeyer, E., et al., German Patent Applications,
-DE3906724 (“Dyeing process“, 1998: granted, 2009: CEASED/NON-PAYMENT OF THE ANNUAL FEE),
-DE4200352 (” PROCESS FOR APPLYING SUBSTANCES TO FIBRE MATERIALS AND TEXTILE SUBSTRATES“, 2002: DISPOSAL/NON-PAYMENT OF THE ANNUAL FEE)
-DE4202320 (“Impregnating substrate by contact with supercritical fluid contg. impregnant – followed by conversion of fluid to subcritical state “, 2002: DISPOSAL/NON-PAYMENT OF THE ANNUAL FEE)
-DE4344021 (“Disperse dyeing of synthetic fibres in supercritical medium”, 2009: CEASED/NON-PAYMENT OF THE ANNUAL FEE )
legal status obtained form inpadoc database - Desai, P .: “Sustainable Innovation Waterless Dyeing with SCF Technology” conference presentation ITMA 2015
- Woerlee, G., Fernandez Cid, M.V., “What Could not be done: Industrial CO2 dyeing”, AATCC Proceedings of the Annual International Conference & Exhibition; 2014 109-116
- Sicardi, S., Frigerio, M., PCT patent application WO0104410
- Fernandez Cid, M, V. et al. (Feyecon BV), European patent application no. EP1834031
- Fernandez Cid, M.V “Cotton Dyeing in Supercritical Carbon Dioxide”, Delft University of Technology, Dissertation, 2005