Enzymes – an alternative for wet processing of denim
Garment wet processing is gaining popularity since several years. Especially for denim fabrics the treatment of garments is common, because of certain effects which can be only carried out on a ready-made garment and not on a flat fabric. Apart from washing and cleaning, it can impart artistic and innovative look to the garments.
However, textile wet processing using chemicals is one of the pollution causing processes in the mills. Denim garment manufactures use numbers of acutely toxic chemicals of which many are classified as hazardous by the WHO.[1] Several denim brands have committed to eliminate the release of all hazardous chemicals throughout its entire supply chain and products. In response to the Greenpeace Detox campaign, a group of major apparel and footwear brands and retailers made a shared commitment to help lead the industry towards zero discharge of hazardous chemicals (ZDHC) by 2020.[2] Denim wet processing with enzymes is a possible alternative, which can at the same time reduce energy costs, water consumption and the eluent load.
Introduction
The use of enzymes allows the development of environmentally friendly technologies in processing and strategies to improve the final product. The biotechnology industry continuously develops innovative enzymes with unique performance features for existing and new applications. Enzymes aim to provide in the complete process a reduction of process time, chemical and energy consumption, in compliance with sustainable developments.
The technical background of enzymes was descripted in an earlier report.[3] This report gives an overview of the use of enzymes compared to traditional applications in the garment process of denim fabrics. Usually the following sequence is applied:
Desizing
For fabrics made from cotton or blends, the warp threads are coated to prevent threads breakings during weaving. Although many different compounds have been used to size fabrics, starch and its derivatives have been the most common sizing agent for denim fabrics. After weaving, the size must be removed again in order to prepare the fabric for dyeing and finishing.
that enzymes are environmentally friendly.
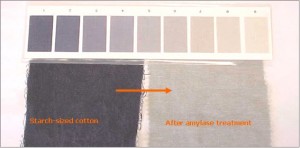
Scouring
A very important process is scouring. In this process, non-cellulosic components from native cotton are completely removed. Scouring is the process of purifying cotton fabrics from impurities such as wax, pectin, hemicelluloses and mineral salts. Pectin acts like glue between the fiber core and the waxes which can be destroyed by an Alkaline Pectinase Enzyme. Scouring provides to a fabric a high and even wet ability so that it can be bleached and dyed successfully.
Today, highly alkaline chemicals such as caustic soda are used for scouring. These chemicals, under harsh conditions, not only remove the non-cellulosic impurities from the cotton, but also attack the cellulose leading to heavy strength loss and weight loss in the fabric. Furthermore, using these hazardous chemicals result in high COD (chemical oxygen demand), BOD (biological oxygen demand) and TDS, in the waste water
In general, cellulase and pectinase are combined and used for bio-scouring. Recently enzymatic scouring process are used in textile wet-processing in which all non-cellulosic components from native cotton are completely or partially removed. After this bio-scouring process, the cotton has an intact cellulose structure, with lower weight loss and strength loss. The fabric gives better wetting and penetration properties, making subsequent bleaching process easy and as a result giving much better dye uptake. .Using textile enzymes instead of hazardous chemicals for bio-scouring, the BOD (biological oxygen demand) and COD (chemical oxygen demand) of enzymatic scouring process in the waste water are only 20-45 % and the TDS (total dissolved solid is only 20-50%, as compared to alkaline scouring (100%).[5]
Combination of Desizing and Scouring Process
To integrate the desizing with the bioscouring process, the availability of an enzyme with broad operational windows is desirable. The operational pH for most enzymes available for these processes are in the acidic (4–7) or alkaline (7–9.5) range, while they all inactivated at elevated temperatures above approximately 50–55°C.[6] . For this integrated process the xylanase enzyme offers good application conditions. Xylanase is a well-known product of the paper and pulp industry. It is used for the degradation of starch to lower viscosity, aiding sizing and coating paper. Xylanases reduce the bleaching process required for decolorizing.[7] This enzyme is active over a broad range of pH ranging from 5 to 10 and is thermo stable up to 70°C that makes it suitable for application in textile industry.
Enzymatic desizing of cotton fabrics is most efficient at 60°C and at pH 7.0. During bioscouring, the significant weight loss is observed when chelating and wetting agents are combined with xylanase. Addition of EDTA (a strong metal complexing agent) results in higher weight losses of cotton fabrics. Adding chelating and wetting agent to the enzyme solution can accelerate the effect of the treatment enormously, indicating the synergistic effect of the enzyme and EDTA applied together in one treatment bath. EDTA modifies the substrate structure by removing the calcium ions from the cross bridges that link the macromolecules in pectin to one another or pectin to other polysaccharides., therefore, when applied simultaneously with the enzyme seems to assist in the creation of free and accessible areas for the enzyme present.[8]
Stonewash / Denim-Finishing
Many jeans garments are subjected to a wash treatment to create an appearance of a cloth which has already been worn for a longer time and washed several times. Stonewash treated jeans show a distinctive abrasion; especially on seams edges. In addition the handle of the jeans becomes pleasant and soft. The change in the color depth of the denim depends on the treatment time, with longer wash times the shade becoming paler.
In the traditional stonewashing process, the blue denim was faded by the abrasive action of pumice stones on the garment surface. The stonewash process can be carried out with or without stones. This gives certain advantages and disadvantages:
Advantage | Disadvantage | |
withpumice stones |
|
|
Withoutpumice stones |
|
|
Nowadays, denim finishers are using a special cellulase enzyme. Cellulase works by loosening the indigo dye on the denim in a process known as ‘bio-stonewashing’. A small dose of enzyme can replace several kilograms of pumice stones. The use of less pumice stones results in less damage to garment, machine and less pumice dust in the laundry environment.
By the use of pumice stones the abrasion effect can be influenced by the amount of stone, use of new or used stones and the treatment time. In the bio-stonewash the strength of abrasion depends on the amount and type of the used cellulase and the washing time.
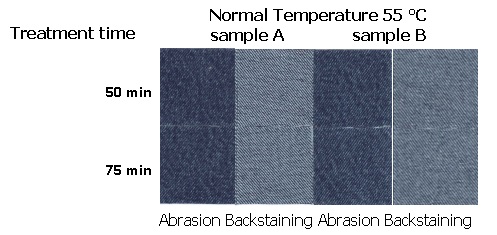
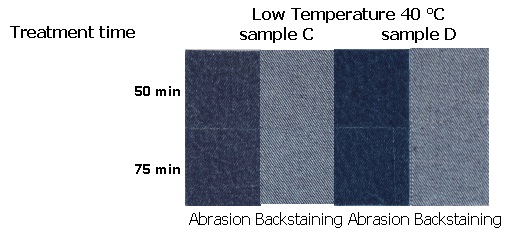
In the figures the difference between some samples at normal temperature (55 °C) and low temperature (40 °C) is visible. There is a huge variety of different cellulose types available, which base on different natural strains or genetically modified organism. Some of the cellulases need only 50 min for the whole process, others can increase the abrasion effect over longer processing time. Some special types can be used in both temperature ranges with similar effects.
Neutral cellulases usually contain buffer systems and small amounts of dispersing agents. Cellulase systems have a very specific pH range, at which they have maximum activity. Controlling the pH is extremely important and should be accomplished by use of a true buffer chemical and not by adjusting the water with an acid or alkali.A buffer is a combination of chemicals that will maintain a desired pH range. The dispersing agent should prevent that the released indigo stains the white weft and reduce the contrast between the blue warp and white weft.
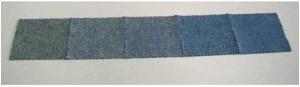
The backstaining effect depends also on the pH range of the liquor. This effect is as lower as the pH is neutral. Under acid conditions the backstaining increase extremely. That is the reason for the use of neutral cellulases instead of acid cellulose, which are much cheaper.
Bleaching
As discussed in a previous report there are many different procedures for bleaching denim materials.[10] Bleaching with sodium hypochlorite is by far the most common bleaching process. It is used when the indigo’s color needs to be lightened as required by fashion, as well as clean up the pocket linen and the inner face of the jeans (weft). This particular bleaching process is preferably used whenever a strong contrast between blue and white fibers is desired, since it gives the bluest cast of all bleaching processes. Moreover, this process is very cost-effective. However, a major disadvantage is that the AOX content, a measure of organic halogen compounds, often exceeds the permitted effluent pollution. Other problems are the damage of the fiber, especially by containing elastic fibers.
Laccases are useful enzymes for an ecofriendly bleaching process of blue denim. The advantage of this enzyme is the specific treatment on the indigo dyestuff and not of the fiber itself. This enzyme breaks down the indigo molecule, without affecting other dyestuffs like sulphur, reactive or direct dyes. The laccase bleaching process has the following advantages:
- denim fibers are not attacked during the fading process
- tendency to a grayish or antique shade (sodium hypochlorite a light bluish cast)
- no damage of elastic fibers, leather labels or metal trims
- no formation of halogenated byproducts
- indigo oxidation byproducts are easily biodegraded in a waste water treatment
- considerable reduction of chemicals, water, time and energy
Laccase enzymes are normally used with a mediator, which increase the low redox potential of the enzyme. The most used mediators are also toxic, but different companies are searching for a natural and less polluting mediator. [11] Another problem is the storage under mild conditions to avoid activity loss of the enzyme.
Bleach Clean-up
Laccases cannot be used for bleaching of black denim, toppings or bottomings with sulphor dyes, because of the specific treatment of the indigo dyestuff. For such denim materials an ecofriendly alternative; the bleaching process with hydrogen peroxide is known. Hydrogen peroxide is a chemical compound, which reacts as an oxidizing agent. Bleaching with hydrogen peroxide is typically chosen for denim articles whenever a high whiteness is requested. But also black denims are usually bleached with hydrogen peroxide, because it avoids a yellowish tone, as it is obtained in case of hypochlorite bleaching.[12] For denim bleaching are the bleaching chemical H2O2 and alkali as activator preferred. Stabilization of the hydrogen peroxide is of fundamental importance to achieve a uniform bleaching effect.
The traditional method is to neutralize the bleach with a reducing agent and two rinse bathes, but the dose has to be precisely controlled. But residues of peroxide can cause catalytic damages and interfere with the dyeing process.
A thorough ‘bleach cleanup’ is necessary. Catalases present a more convenient alternative, because they are easier and quicker to use. A small dose of catalase is capable of breaking down hydrogen peroxide into water and oxygen. Compared with the traditional clean-up methods, the enzymatic process results in cleaner waste water and reduced water consumption.
Finishing
There are two different ways for the finishing process:
- denim finishing
- bio-finishing
Denim finishing is normally made with the stone-wash process, where the Cellulase works by loosening the indigo dye on the denim. So for denim fabrics the finishing is more an afterscouring. The afterscouring removes unfixed indigo from the surface and improve the contrast between warp and weft. Remaining enzymes should be removed to avoid a decrease of tensile strength during intermediate storing under humid conditions.
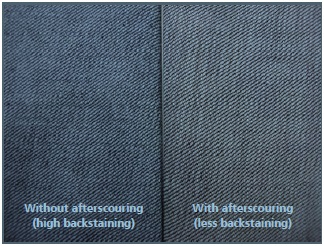
Bio-fishining (also known as bio-polishing) is an enzymatic finishing technology, mainly used for cellulose-containing fabric and garment finishing. Enzymes lint surface of the fabric in a controlled partial hydrolysis occurs, greatly reducing fiber fuzz and pills from the fabric surface.
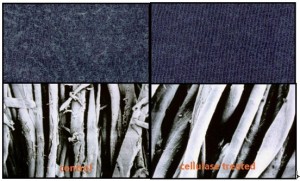
This process is made with acid cellulose (Stonewash with neutral cellulose) and is normally not used for denim fabrics, because the acid cellulose has a much higher abrasion and is made under acid conditions (pH 5). The following of this process is a strong backstaining and the risk of strength loss increase.
Conclusion
Today, various types of enzymes are employed in manufacturing food, fuel, clothes, and other products. Most amylases, cellulases and xylanases are used in the paper and pulp industry; lacases in the waste water treatment; catalases in the rubber industry. Especially a huge amount of cellulases are developed for the biofuel industry. The use of enzymes on the industrial scale has been imperfect, in spite of its exceptional catalytic properties. Why should they not use for the standard denim manufactures?
This report shows that the entire wet garment processing of denim fabrics can be made with enzyme products. The use of enzymes in the denim finishing process is an example of the use of biotechnology, which allows the development of environmental friendly processing technologies to improve the final product. These products can replace numbers of actually toxic chemicals, including formaldehyde and aromatic solvents, and at the same reduce the total BOD, COD and TDS load in the effluent. Wet processing with enzymes changes the concept of textile processing from high energy consuming and pollution oriented on to a green process with advantages such as reduction in process temperature and reduction in effluent load. This strategy change has also a double effect: The employee in the wet processing plant has to handle less hazardous and toxic material, which Greenpeace made public during the last years. In the scope of the Detox campaign Greenpeace called upon leading fashion brands to replace hazardous chemicals with hazard-free chemicals in their supply chain. Greenpeace published a report that 70% of Chinese and Mexican waterways are contaminated with hazard chemicals caused by international textile production. The discharge of the textile auxiliaries are blacklisted as a danger to the environment and the public health.[13]
On the other hand the change in the wet production gives the brands the possibility to fulfil their target is the ZDHC project. The philosophy of ZDHC is to bring no harmful chemicals in the production process, which must be removed out of the water and air cycle. If there is only a look on the wet processing of denim fabrics, it must be considered, which products are used in the whole processing steps. If no harmful products are used during the production, no chemical can found on the final products, which are sold all over the world[14].
Process | Standard process | Alternative enzyme |
Desizing | Washing with high temperature | Amylase, Lipase, Xylanase |
Scouring | Caustic soda | Pectinase, Cellulose, Xylanase |
Stone-wash | Washing with pumice stones | Neutral Cellulase |
Bleaching | Sodium hypochlorite | Laccase |
Bleach clean-up | Sodium bisulfite, 2-3 rinse bath | Catalase |
Biopolishing | – | (Acid Cellulase) |
Finsihing | Softeners | Bio-stone-wash |
Further research is required for the implementation of commercial enzyme based processes for the bio-modification of synthetic and other natural fibers such as standard cotton, wool and silk. An active field of research is the search for new enzyme-producing micro-organisms and enzymes extracted from extremophilic micro-organisms.[1]
A principal hurdle in the commercialization of enzymatic processes is the bulk production of enzymes at a cost effective rate. In order to meet this goal, such strategies should be explored by which cost-efficient bulk production can be achieved. Therefore, the coming years will see advancement in production methods to exploit such microbial species that can easily metabolize the available waste material by using the simplest techniques at affordable prices. Much progress has been made in understanding the basic mechanisms of different enzymes and in engineering their properties. In order to bring such a revolution in production and industrial applications to biotechnologists, microbiologists, and biochemists should work together for the future. There is still considerable potential for new and improved enzyme applications in future textile processing. According to market analysts, the global enzyme market is expected to reach U.S $ 4.3 Billion by 2015. With the growing interest in the field of immobilized enzymes and advances in biotechnology, the enzyme market is expected to surpass this number in the coming years. [1].
[1] http://www.textiletoday.com.bd/magazine/722
[2] Roadmaptozero.com: About ZDHC
[3] Enzymes – an ecofriendly alternative for the textile industry?
[4] Novozymes presentation
[5] Enzyme and Its Applications in Textile Processing – Textile Learner
[6] Lenting HBM, Warmoeskerken MMCG. “A fast, continuous enzyme-based pretreatment process concept for cotton containing textiles.” Biocatal Biotransform. 2004;22(5/6):361–368. doi: 10.1080/10242420400024557.
[8] Losonczi A, Csiszar E, Szakacs G, Bezur L. Role of the EDTA chelating agent in bioscouring of cotton. Text Res J. 2005;75(5):411–417. doi: 10.1177/0040517505053812.
[9]http://www.ncsu.edu/bioresources/BioRes_03/BioRes_03_4_1377_Dhiman_SB_Indust_Appl_Microb_Xylanases_Rev.pdf
[10] Jeans bleaching – advantages and risks of different bleaching processes – part 2
[11]S. Rodrigues-Couto, „Laccases for denim bleaching: An eco-friendly alternative”, The open Textile Journal, Vol. 5, 2012, 5, 1-7
[12]H.K. Rouette “Encyclopedia of Textile Finishing“, Springer-Verlag Berlin Heidelberg New York, ISBN 6-84569-065-6, 2002
[13] Greenpeace.de: Kampagnen
[14] Roadmap to Zero Discharge of Harmful Chemicals “Draft: joint roadmap version 2” March 2013
Enzymes – an alternative for wet processing of denim http://t.co/dShSD9ViGe