Nobody knows what the future will bring and how fast. The future of coloured wool may be coloured sheep after all – Chinese scientists in Urumqi have are using already gene editing techniques to alter the coat colours of sheep[1]. However, the wool industry is a very conservative industry and the changes may not be so disruptive anytime soon.
Real and perceived environmental risks, pressure from retailers and legislation, are today the driver for change. The main challenges are metals in dyeing, especially related to chromium (VI), absorbable organic halogen (AOX) in shrink-resist finishing and pesticides in mothproof finishing. These environmental challenges and technical alternatives in wool dyeing & finishing are discussed in this article.
Wool Composition and Dyeing
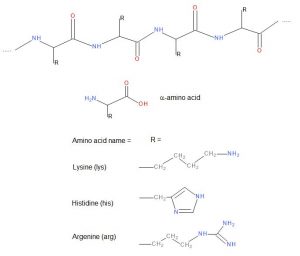
Wool is an animal fibre made of polypeptides, a biodegradable natural protein fibre. Wool is mainly from sheep hair. Other wool fibres are for example cashmere, angora and alpaca. Further examples of protein fibres are human hair and silk. Proteins are built of amino acids connected to each other by peptide bonds.
The dyeing and finishing of wool is based on several physical and chemical effects such as electrostatic interactions, van der Waals interactions and entropy driven hydrophobic interactions[2].
Amino groups in wool play an essential role in these interactions. The amino groups can form metal complexes with metals in dyes, form electrostatic interactions between protonated ammonium groups and sulfo groups in anionic dyes, and react with reactive dyes to form covalent bonds.
The amino acids in wool which carry amino functions are lysine (3.1 mol%), arginine (6.8 mol%), histidine (0.9 mol%) and terminal primary amino groups2. In addition, wool has many carbonamido groups in peptide bonds which can form hydrogen bonds with dyes.
Dyes for Colouration of Wool
Wool can be dyed using acid, metal complex or reactive dyes. Some of the main differences between these dyestuff classes are shown in table 1.
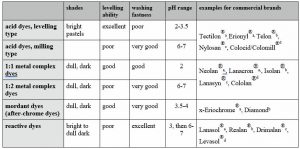
Acid and Metal Complex Dyestuffs for Wool
Acid dyes are dyes with conventional chromophores, mostly azo dyes, having one or more sulfo groups to achieve water solubility. Depending on molecular size the substantivity and migration varies; technicians speak of levelling and milling types of acid dyes.
The levelling performance is important for selection of the machinery. Good levelling dyes can be applied in hank dyeing of yarn and piece dyeing on the winch. Dyes with lower migration should be applied on package machinery for yarns and soft-flow jet machines for piece dyeing.
Metal complex dyes are today in most cases based on Chromium (Cr) or Cobalt (Co), mostly Chromium. Metal complex dyes are azo dyes having two OH substituents in ortho position adjacent to azo linkages, being able to form a chelating complex with metals. These complexes are very stable and exhibit high fastnesses. 1:1 and 1:2 complexes are both used, the figures indicating the ratio of metal to dye molecules (Examples see Fig. 3).
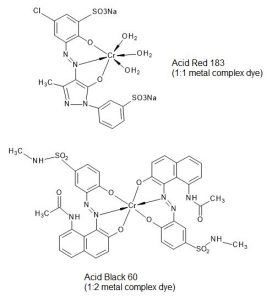
Intelligent Mixtures
Mixtures of acid, metal complex and reactive dyes, respectively selections thereof, are also very common in the market. The most famous ones are Lanaset® dyes, launched 30 years ago by Ciba. These dyes comprise metal-complex, acid and reactive dyes in one range. Lanaset dyes are claimed by Huntsman to be the most successful range in the history of wool dyeing[3]. Dyeing is at isoelectric point of wool (pH 4.5) in good quality (no tippy dyeings), which helps to preserve wool quality. A wider shade range is available compared to classic metal complex dyes. In the meantime, various competitors have copied the concept, e.g. Supralan® by DyStar, Lanasyn® CF by Archroma and the Levaset® range by Colourtex.
Mordant Dyes
Although wool is less than 5% of global fibre consumption, of which 65% is clothing, wool is very important for high-quality formal wear in which colour fastnesses are of crucial importance. Dyes having excellent fastnesses are mordant dyes, in particular after-chrome dyes.
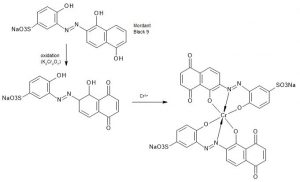
A mordant dye is a dye that becomes fixed on a fibre by forming an insoluble compound with a mordant. In wool dyeing, the common mordant is dichromate.
The most famous mordant dye for wool is Mordant Black 9, (e.g. Diamond Black PV by DyStar). Fig. 4 shows the chemical structure after forming a chromium complex.
The Chromium Challenge
Environmental scandals linked with hexavalent chromium become known to the broader public by the case of the American environmental activist Erin Brockovich, featured in a famous Hollywood movie by actress Julia Roberts. Cases in recent years in USA[4] and UK[5] brought up again the issue of chemical pollution linked with chromium. A factory in south-west China – Luliang Chemicals – was caught dumping 5,000 tonnes of toxic chromium tailings next to an important drinking source, which has brought to light years of illegal disposal of factory waste[6]. Greenpeace has stressed the poisoning of the Pearl River Delta in Guangdong, China, and reported critical levels of heavy metal, including chromium (Fig. 5).[7]
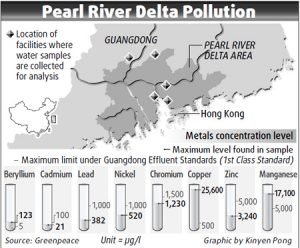
Hexavalent chromium is used in tanneries in the leather industry and in the textile industry in the processing of wool. Dyeing wool with chrome (mordant) dyes, which are applied with potassium or sodium dichromate, is coming increasingly under pressure. The European Chemicals Agency (ECHA) has included dichromate into the list of substances of very high concern (SVHC). Dichromate is hexavalent Chromium (Chromium VI), which is recognized as a human carcinogen. Chromium compounds are linked to lung cancer. Chromate-dyed textiles and chromate-tanned leather can cause or exacerbate contact dermatitis.
Apart from legislative pressure, brands and retailers are asking their suppliers if they use any product listed under SVHC. The ZDHC group has blacklisted Chromium and banned from intentional use in their manufacturing restricted substance list[8].
Huntsman has proactively discontinued their chrome dyes range Eriochrome already in 2008, while many competitors have continued to supply the market. The main reason for continued usage was the outstanding performance of chrome dyes which suppliers claimed could not be matched with any other coloration technology. DyStar, a subsidiary of the Chinese Longsheng group, points out on their website: „Until now, retailers have been unable to substitute Black PV types due to their processing fastnesses used in wool finishing (potting and cross dyeing). Even though Black PV types can be dyed without ecological and health and safety issues, textile manufacturers are pressured by retailers to avoid mordant dyes“[9].
Due to increasing pressure of legislation and retailers, the market moves away from after-chrome mordant dyes, primarily to reactive dyes.
Reactive Dyes for Wool
Chemical solutions for reactive dyes suitable for wool are shown in Fig. 6. Let us look into the history of these dyes. It may be a surprise even to technically experienced people: reactive dyes for wools are in fact older than reactive dyes for cotton. Supramin Orange R dye, based on chloroacetamido, is traced back to the 1930s to IG Farben in Germany[10]. The covalent dye-fibre bond was not recognized and the dye was labeled as acid dye (Acid Orange 30).
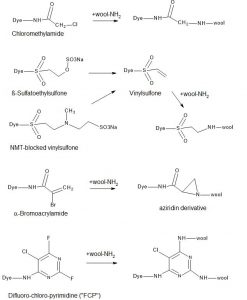
Hoechst had developed a range of reactive dyes for wool (Remalan), based on vinylsulfone chemistry, while not recognizing the potential for cotton at the time; it was not understood that a covalent dye-fibre bond was formed in the case of cotton; only after ICI launched their Procion® MX dyes, the potential of reactive dyes for cotton was fully recognized.
A historical patent of Hoechst[11] filed in 1949 disclosed vinyl sulfone reactive dyes, mostly applied on wool. This patent, the mother of today’s modern reactive dyes, already illustrated Reactive Black 5 dyed in 6% on wool (example 50). The inventors Heyna & Schumacher received in 2000 posthumously the Perkin Medal by the Society of Dyers and Colourists for their groundbreaking work.
In the 1950s, Hoechst´s Hostalan® range for wool was based on vinylsulfone as active fibre reactive group. However, it was not applied as today’s sufatoethylsulfone, but instead as N-Methyl taurine blocked vinylsulfone system.
Ciba launched Lanasol dyes based on α-bromoacrylamide as fibre reactive group, supported by a leveling agent Albegal® B, applied in slightly acidic conditions. A wide shade range can be covered with the trichromatic dyes Lanasol Yellow 4G, Red 6G and Blue 3G. These dyes have good lightfastness and very good fibre levelness. Major applications include yarn dyeing (package and hanks), particularly in the Chlorine-Hercosett process for machine-washable wool, loose stock and top dyeing.
20 years ago, Ciba launched Lanasol CE dyes with the target to replace chrome dyes. These dyes are designed to achieve economical deep shades with high wet fastness. But there was still a performance gap in dark shades and black compared with chrome (mordant) dyes. But finally, these gaps were closed with new dyes from the R&D pipeline.
Chrome Black Replacements by Reactive Dyes
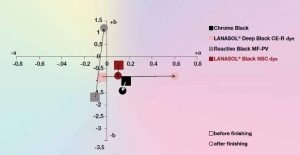
As mentioned above, the market moves away from after-chrome mordant dyes to reactive dyes. Now, with new additions in the area of reactive blacks during recent years, having outstanding fastness properties to overcome performance gaps, the market may be ripe for a permanent change. In particular, the new dyes Lanasol Black NSC by Huntsman[12] and Realan MF-PV by DyStar („a quantum leap“)[13] are worth mentioning. DyStar claims outstanding fastnesses, in almost all ratings as good as after-after-chrome dyes, except inferior light fastness. Huntsman claims in their Black NSC, in which „NSC“ stands for no shade change, a remarkable similarity of the shade after finishing compared to chrome black, distinctively superior to their competition[14](Fig. 7). With these news dyes, although the wool industry is a very conservative industry, amidst pressure from legislation and retailers a conversion of chrome dyes seems than ever before.
Mothproofing Finishing
Certain insects (e.g. Tineola bisselliella) can digest proteins while attacking the peptide bonds of the main protein chains in wool. Insecticides (mothproofing agents) were developed to tackle this challenge.
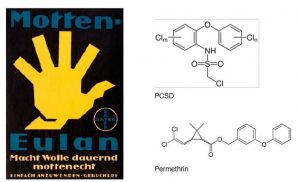
Famous mothproofing insecticides of historical significance are the products of the Eulan® brand[15]. The brand can be traced back to 1921, originally by Bayer AG´s predecessor companies Friedrich Bayer & Co. and IG Farben (Fig. 8). The brand was later transferred to spin-offs companies Lanxess and Tanatex.
Eulan has contained various chemistries related to insect repellency15. Historically, polychlorinated diphenylethers (Eulan WA new/U33 from Bayer, discontinued in 1988) were used for decades. These chemicals are highly persistent and poorly degradable. Today the major wool mothproofing agent is Permethrin, a synthetic pyrethroide (Fig. 8). It has low mammalian toxicity and good washing fastness, but a relatively high aquatic toxicity which has led to effluent restrictions. Product alternatives having less aquatic toxicity compared to Permethrin are Bifenthron, developed by Wool Research Organisation of New Zealand and Chlorfenapyr by Catomance/ AgResearch.
A comprehensive review article on the eco consideration in wool finishing, including further aspects, was published by Ingham et al.[16]
Shrink-Resist and Anti-Felting Finishing
The surface of natural wool is hydrophobic. As a consequence, in aqueous medium wool fibres tend to aggregate, and under mechanical action they move to their root ends. Felting and shrinkage is observed.
Traditionally, wool is processed using aqueous chlorine solution to achieve an anti-felting effect. This process is environmentally problematic due to release of adsorbable organic halogen (AOX) which is related to the use of chlorine.
Alternatives are peroxide derivatives and plasma treatment which can provide an anti-felting effect on wool without incurring environmental problems. After plasma treatment the hydrophobic layer is oxidized and partially removed; the result is an anti-felting and shrink resistance effect. The anti-shrinkage effect of plasma is less than traditional treatment, however, in combination with resin finishing it is acceptable[17].
Conclusion
The main environmental challenges in wool dyeing & finishing are the use of hexavalent chromium in the dyeing process, AOX in anti-felting/ shrink resist finishing and mothproof agents. The alternatives discussed in this article include the use of new generation reactive dyes, plasma treatment and new generations of more environmentally friendly mothproof agents.
A compressed version of this article was published in the journal International Dyer & Textile Finisher 2/2019, 22-25.
References
[1] Zhang,X. et al., Scientific Reports 7, 8149 (2017)
[2] Lewis,D.M., Handbook of textile and industrial dyeing, Vol 2. Application of Dyes, Part I. The Coloration of Wool, edited by M. Clark, Woodhead Publishing, 2011
[3] Huntsman presentation: „Turning risks into opportunities – how to dye wool sustainably“
[4] New report finds ‘Erin Brockovich’ chemical in US drinking water
[5] Erin Brockovich pollution’ on River Clyde
[6] Meng Si: „On Yunnan’s chromium trail“ (2011), https://www.chinadialogue.net/article/show/single/en/4493-On-Yunnan-s-chromium-trail
[7] https://www.greenpeace.org/eastasia/Global/eastasia/publications/reports/toxics/2010/poisoning-the-pearl.pdf, http://www.china.org.cn/environment/2009-10/29/content_18787997.htm
[9] Realan Black MF – PV: A quantum leap in the dyeing of black on wool
[10] Lewis, D.M., „Dyeing wool with reactive dyes“, chapter 9 in The coloration of wool and other keratin fibres, edited by Lewis, D.M., Rippon, J.A., Wiley (2013)
[11] Heyna,J., Schumacher, W., German patent DE965902 (1949)
[12] LANASOL® CE – pioneering replacement of chrome dyes since 20 years
[15] Homolka,M., „Eulan – ein Biozid gegen Keratin-Schädlinge und seine Relevanz in musealen Sammlungen“, Stiftung Deutsches Historisches Museum (2015), www.dhm.de
[16] Ingham,P.E., McNeil,S.J., Sunderland,M.R., „Functional finishes for wool -eco considerations“, Adv. Mater. Res. 441 (2012), 33-43
[17] Thomas, H., „Plasma modification of wool“, chapter 9 in „Plasma Technologies for textiles“, Woodhead Publishing in Textiles, edited by Shishoo, R., Cambridge (2007)
testing
Coursiify 6-Figure In 60 Days LIVE Event
Get VIP access to our live mastermind event and copy n’ paste our Coursiify underground system we use to make 6-figures in 60 days.
This alone is worth 5x what you will pay today, and it’s yours for free!
(Value $1997) https://ext-opp.com/Coursiify